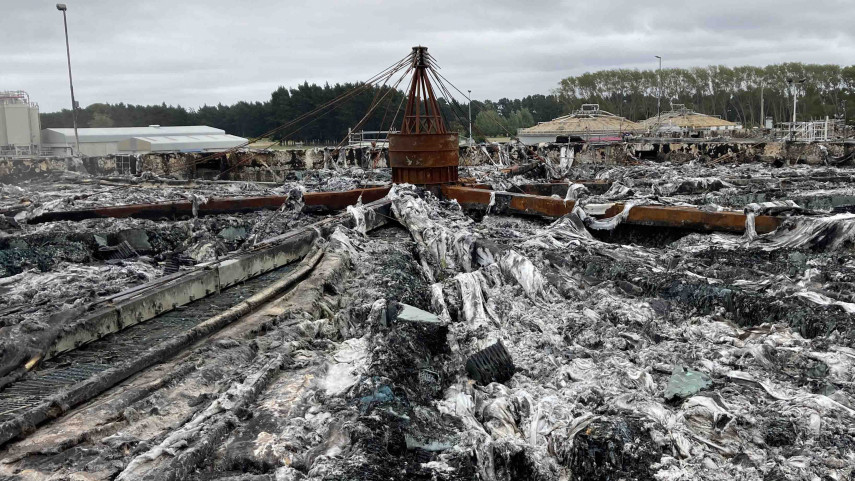
The stench from the fire-damaged Christchurch Wastewater Treatment Plant is seriously impacting on the wellbeing of nearby residents. Here we answer some more of your questions about why the plant is still in this state and what we’re doing about it.
It is nearly six months since the fire at the treatment plant. Why does it smell the way it does?
The Mayor and Councillors will get a full briefing on the situation at the Christchurch Wastewater Treatment Plant and the work that is being done to address the odour issues at 9.30am, Thursday 28 April.
The briefing will take place at the start of the Finance and Performance Committee meeting and will be live-streamed so members of the public can also hear first-hand what is happening.
The Committee will also receive a written report on the recovery effort.
You can watch the live-stream here.
The smell is coming from two sources – the trickling filters where the fire occurred and the oxidation ponds. We’re working to have both issues resolved by the coming summer.
If the fire was in the trickling filters, why are the oxidation ponds smelling?
The fire severely damaged the trickling filters so we lost a critical part of our wastewater treatment process. As a result poorer quality effluent was being discharged into the oxidation ponds, so the ponds then began to smell. If you remember Bromley in the 1960s and 70s, that smell would be very familiar.
What have you done to stop the ponds smelling?
Immediately after the fire, we began adding hydrogen peroxide to the wastewater flowing into the oxidation ponds to maximise the oxygen saturation in the water and minimise the potential smells.
Churning additional oxygen into the wastewater is key to improving the quality of the effluent being discharged to the oxidation ponds. We have sourced aerators from different parts of the world to do this and have converted two of the plant’s four clarifiers into aeration basins using this equipment.
Aerators are helping to reduce the smells from the oxidation ponds.
The equipment arrived in the country in late February, was assembled and then lifted into the basins in mid-March. The aerators were turned on in early April. It will take between four and six weeks for the aeration basins to adjust and stabilise to the new treatment process. we expect the odours coming from the ponds will continue to reduce over this period.
What’s the situation with the trickling filters – why do the smell so badly?
During the 1 November 2021 fire, the roofs on the trickling filters were destroyed. Immediately after the fire the burnt plastic media housed inside the round concrete trickling filters gave off an acrid smell.
That smell largely went away but over time the material inside the filters has started to putrefy. When it rains the filter media gets wet and the organic matter trapped within the media putrefies, releasing a pungent odour until it dries.
Our top focus now is on removing the filter media as soon as possible so we can get rid of the smell.
Why hasn’t that happened before now?
We had to carry out an extensive investigation into the fire and the damage it caused and work through an insurance claim, all of which has taken time. Other parties involved have also been carrying out their own investigations.
We needed to fully understand the damage to inform our remedial options, but our insurer has now agreed that the filter media needs to be removed regardless of whether the end result is a repair or a rebuild.
What’s the next step?
We’re going to directly appoint a contractor - rather than to go out for tenders – to remove the material in the trickling filters. This is designed to save time. The work will be funded from an interim $10 million payment we received from our insurers in late November 2021.
What is the material inside the trickling filters?
The bulk of the material is a mix of plastic and biomass, which was used to help treat the sewage being processed through the plant. Some of the biomass within the tricking filters is rotting and that is causing the stench.
Why is the smell worse on some days compared to others?
Wind, humidity and temperature all influence how odours from the plant are spread. While a strong breeze helps dilute and disperse the odour, conditions with light or no wind, such as the still nights experienced lately, allows the odour to linger.
Surely there must be a temporary fix?
Council staff have investigated a range of options – including some that Councillors have put forward – to get rid of the smell, at least temporarily, but none of them stack up. The trickling filters are huge structures and any temporary measure would require many of same initial steps as removing the material inside
We also need to think about how any temporary measures could impact on the day-to-day running on plant, which has to keep operating.
Why can’t you just bulldoze the trickling filters and cart everything away?
We may end up having to demolish the filters. However, the material inside the filters is classed as hazardous material and the concrete structures are huge – each is about three storeys high and 55 metres wide.
We need to make sure that whatever we end up doing is safe for nearby residents, our contractor and the environment.
Why is removing the material from the trickling filters going to take four to seven months?
Removing the material from inside the trickling filters will be tricky because of the height of the concrete structures - they're about three storeys tall.
About 26,000 cubic metres of filter material needs to be extracted - that equates in volume to more than 10 Olympic-sized swimming pools.
It is estimated that setting up the removal operation will take about a month. We think it will then take another three months per trickling filter to completely remove the material. We can only remove the material from one trickling filter at a time because there is not enough space on site to run twin removal operations.
We are working closely with our contractor to see if the process can be sped up. If they can find a methodology that will allow the material to be removed more quickly, without compromising safety, they will use it.
You say the smell might get worse as the material is removed. Why is that?
As material is removed from the trickling filters, fresh media will be exposed to the open air. We anticipate that as the fresh media is exposed, it will potentially release a pungent odour until it is removed.
When the removal work begin?
We want the removal work to get under way as soon as possible so we are fast-tracking our normal procurement processes and appointing a contractor. The contractor we are looking to engage to do the work is well aware of the urgency and has signalled that they will remove the material as quickly as possible.
We hope to make a further announcement in the next 10 days.
Where are you going to put the material that is removed?
The material will be loaded into sealed bins and transported to the Kate Valley landfill where it will be treated as hazardous waste. Kate Valley landfill is operated by Transwaste Canterbury Limited. We will be asking them to work with us to ensure the material can be taken there as quickly and cost effectively as possible.
Have you determined what caused the fire?
Investigations are on-going into the cause and origin of the fire. Due to the complexity of the investigation and the fact other parties are involved, we are not in a position to share any further information at this stage.
What’s happening with your insurance?
We have been in constant communication with our insurer since the fire. The wastewater treatment plant was fully insured Our insurer has accepted our claim but a settlement has not yet been reached. Investigations are still determining whether the trickling filters are a rebuild or a repair.
When are the trickling filters likely to be replaced?
It’s likely to be years before we’re able to fully rebuild or replace the trickling filters.
How are you running the wastewater treatment plant without the trickling filters?
We have modified the plant so that we can bypass the trickling filters.
As mentioned earlier, we have converted two of the plant’s four clarifiers into aeration basins. Once wastewater passes through these new aeration basins, submersible pumps will push the wastewater through to the remaining two clarifier tanks.
The new system is close to being fully commissioned. The new aeration basins will not fully compensate for the treatment work that was previously undertaken by the trickling filters. However, they will greatly improve the quality of the wastewater being discharged into the oxidation ponds and the overall biological health of the ponds.
We will be closely monitoring the water quality in the ponds to assess the effectiveness of the aeration basins. If we need to, we will install more aerators in the oxidation ponds to further improve the water quality.
How can I register my concerns about the smell?
The best thing to do is report it to Environment Canterbury because they monitor air quality. You can call them on 0800 765 588 or you can use the Smelt It app.
You’re also welcome to give our call centre a call on 941-8999.
How can I stay up-to-date with the situation and your progress?
You can subscribe to our e-newsletter at ccc.govt.nz/wastewaterfire.