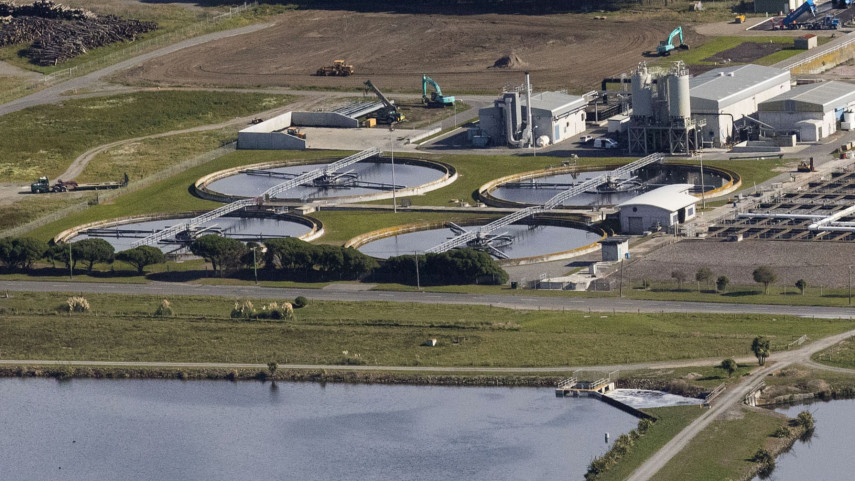
The impacts of the 1 November fire at the Christchurch Wastewater Treatment Plant could be felt for a long time. Here is the most up-to-date information on the repair and mitigation measures that are in place.
Why will it take so long to repair these two roofs on the tanks and replace the filter media?
The damage assessment of the two destroyed trickling filters is still being undertaken. Until this is completed, we don’t know if it’s possible to repair the concrete housing and replace the trickling filter media. If the concrete housing is badly damaged we will look at the options for rebuilding the trickling filters alongside alternative technology.
Assessing the damage is a detailed technical process as we need to remove some of the filter media, without causing further damage to the concrete structure, and then assess the condition of that concrete structure. This is expected to be completed by the end of March 2022. And these structures are huge – 8 metres high and 55 metres in diameter. There’s 12,000 cubic metres of material in each of the tanks that will need to be removed.
Why is there a lack of urgency to fix this problem when the smell is horrible and persistent?
We are working as hard and as quickly as we can and we’re prioritising work that will reduce the odour and ensure the wastewater is treated before being discharged through the offshore ocean outfall. We acted immediately to enhance the operation of the treatment plant by installing polymer dosing of the primary sedimentation tanks (one day after the fire), adding hydrogen peroxide to the wastewater going into the ponds (four days after the fire), and trialling polymer dosing of the clarifiers (two weeks after the fire).
The polymer dosing improves the removal of solids from the wastewater and reduces the load on the ponds. Hydrogen peroxide breaks down into oxygen and water to raise the level of dissolved oxygen in the ponds and reduces the potential for anaerobic conditions. Anaerobic conditions in the ponds generate offensive odours with a distinctive rotten egg smell.
The trickling filters provided around 60 percent of the treatment of organic material in the wastewater and this means that more changes are required to further improve the operation of the plant, to make up for this loss of treatment effectiveness. To this end we’re modifying two of the four clarifier tanks into aeration tanks and adding aerators to ponds.
Has the Council considered ways to speed up the repair process? If not, why not, and when can they start doing that?
We’ve looked at the fastest possible ways to enhance the interim operation of the plant. We will continue to monitor the quality of the wastewater discharge and assess the operation of the whole process, including the oxidation ponds, to minimise the generation of odours.
Our recovery plan for interim operations addresses the efficient removal of organic matter (measured by Biological Oxygen Demand (BOD)) early in the treatment process, which is critical for the management of odour from the plant. We intend to convert two of the four clarifiers into suspended growth aeration basins and install aeration on pond 1. The conversion of the clarifiers to aeration basins is scheduled to be completed by the end of March 2022.
Additional aeration of pond 1 will occur progressively over the next six to nine months – one aerator has already been installed and two more are scheduled to be in by the end of January. We’ve borrowed aerators from around the country and will also need to have some made. This will take time. We may install as many as 16 aerators throughout pond 1.
Will the ratepayers have to pay any of the repair cost?
We’re in discussions with our insurers. Because investigations into the fire are still under way, we’re unable to provide any further information at this stage.
Is there an opportunity for an independent expert to review the lack of progress to date on behalf of ratepayers and recommend solutions?
We have made considerable progress and we’re looking at every opportunity to improve both the wastewater treatment and the odours coming from the plant. We have engaged external specialist consultants to assist our teams to find the best and quickest approach and will continue to explore other improvements to the operation of the plant. We provide regular updates on ccc.govt.nz/wastewaterfire and via the Council’s Newsline site.